Sealing Heads and Induction Cap Sealers
There are three main components to an induction cap sealer; the power supply, the operator interface and the sealing head.
When you purchase an Enercon Super Seal™ cap sealer our team expertly matches the power supply, interface and sealing head to meet your specific application requirements.
Packagers sometimes overlook the importance of the sealing head design. While the power supply plays a significant role, the efficiency of your sealing operation depends on the design of the sealing head. The secret to creating fast, efficient, and consistent seals is the energy transfer from the power supply to the sealing head and into the foil liner. If you don't have the correct design, increasing the power only wastes energy.
There are a number of key application variables taken into consideration when Enercon recommends an induction sealer configuration. These variables include line speed, cap diameter, cap type, and liner type. When any of these variables change you should consult with Enercon to see how your current sealer is equipped to handle the new set up. In some cases no changes to your set up are required. In other cases an adjustment to the power level or line speed will ensure successful sealing. It is also possible that your operation would benefit from a second sealing head designed to better accommodate your additional application.
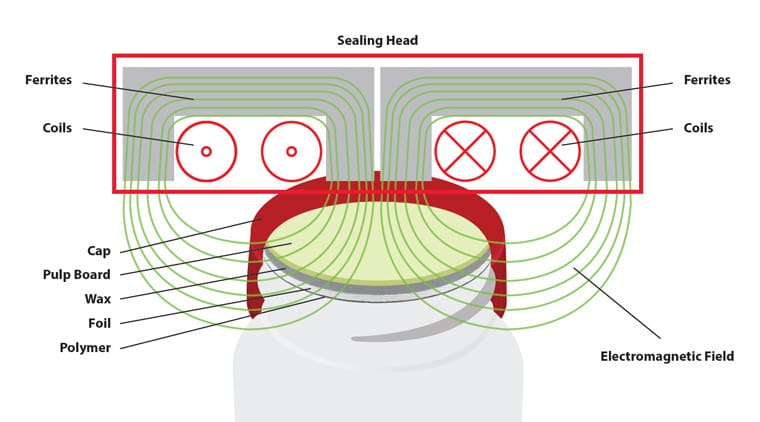
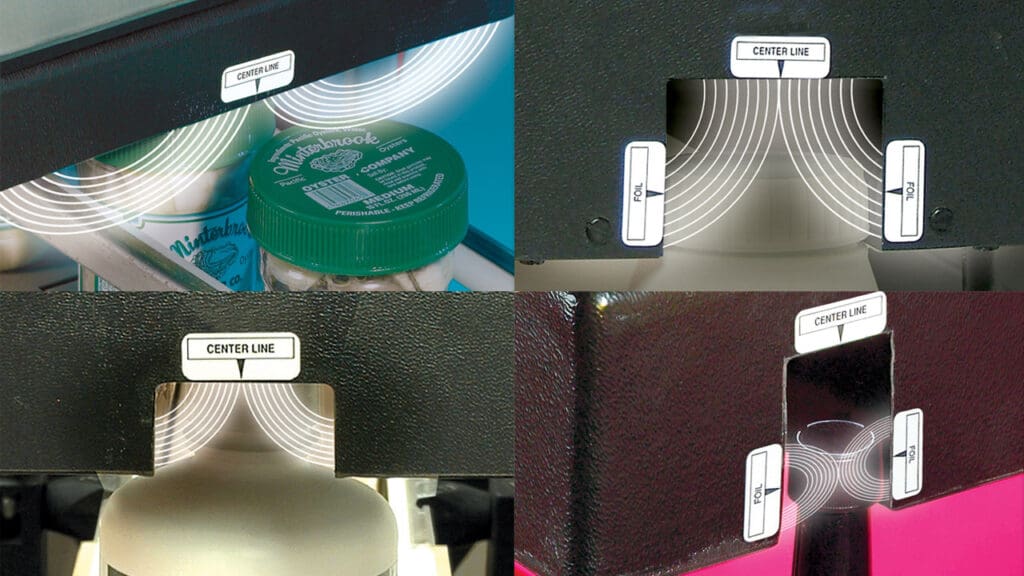
KEY FEATURES Induction Sealing Heads
-
Application variables including cap style, liner size, liner style, container shape & line speed affect sealing head choice.
-
Each version of Enercon's high efficiency sealing heads create a unique induction field to optimize sealing results.
-
Enercon engineers & application experts can recommend the best sealer for your application.